OUR TEAM
With over a century of experience in the hot forged steel industry, we are proud to have highly trained specialists dedicated to the development of the highest quality steel components.
Our team is the fundamental pillar that sustains our track record of quality and reliability. Composed of skilled operators, innovative engineers, attentive sales people, efficient administrative staff and valuable collaborators, each member brings his or her experience and dedication to achieve our common goals.
Our operators are the craftteam who transform ideas into reality, working with precision and care. The engineers, with their technical approach, develop solutions that allow us to move forward and adapt to market demands. The commercial team makes sure that our customers’ needs are always a priority, while the administrative team ensures that everything runs smoothly and in an organized manner.
In addition, our external collaborators enrich our work with their perspective and expertise, helping us to always deliver the best.
At Forjas de Berriz, we form a team that works in a coordinated and efficient manner. We appreciate everyone’s effort and dedication to keep moving forward.
FACILITIES
We have modern and sustainable facilities, recently expanded with improved machinery, easier access for loading and unloading, as well as the installation of solar panels.
HISTORY
FOUNDATION OF THE COMPANY AS A MANUFACTURER OF AGRICULTURAL AND ARMOURY PARTS
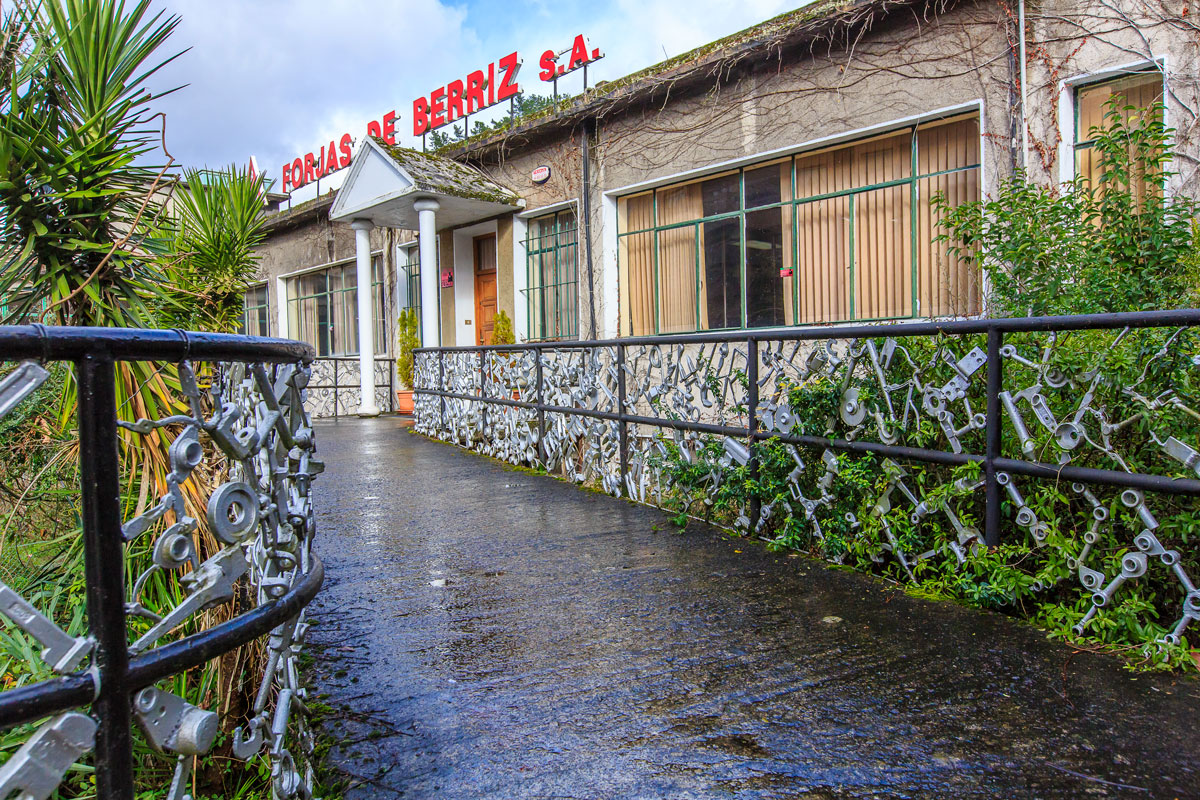
The history of hot forging in Spain dates back to the beginning of the 20th century, and it was then that Forjas de Berriz was founded, an emblematic company in the sector and well known locally.
Forjas de Berriz played a crucial role in the development of various economic sectors at that time, such as construction, armoury and agriculture.
Start of supply to Automotive and investment in first mechanical press: 1600
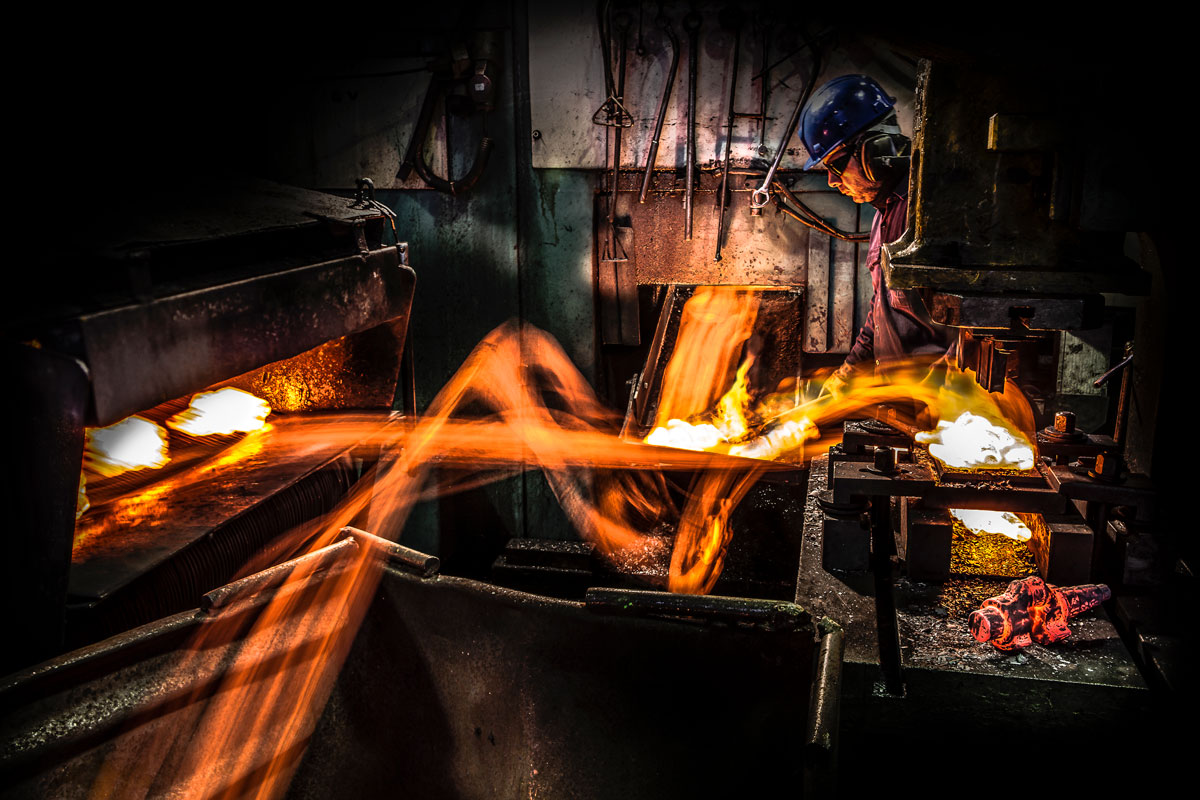
The acquisition of the first mechanical press was a milestone for the company. After years of forging with hammers, this acquisition allowed the company to diversify its offer and supply new emerging sectors, including the automotive industry, a sector that was already feeding the industrial fabric of the area. The demands of this sector and many others made the need for modernization and new investments evident.
PURCHASE OF TWO MECHANICAL PRESSES OF 1600
In the 1990s, the acquisition of two additional presses allowed us to increase production, overcoming previous limitations. This expansion not only increased our operating capacity, but also prompted the hiring of additional personnel, strengthening our workforce. Thanks to these strategic investments, we were able to successfully weather the industrial crisis that so affected the country.
FIRST AUTOMOTIVE-ONLY CERTIFICATION
The certification in the automotive sector was undoubtedly a before and after for the company, it opened the door to access to the most demanding companies in the sector and also allowed us to start exporting to Europe and the USA. This new challenge entailed a great effort on our part.
At this time, the company faced a process of constant evolution, very demanding and with a need for computerization of processes, accompanied by significant investments in specialized software.
CHANGE OF OWNERSHIP AND START-UP AS AN INDEPENDENT COMPANY
In 2008 the founding family decided to sell the company to a group of local businessmen.
Today, it remains in private hands and under family management, which facilitates strategic decision-making.
Although a change of ownership in a company always generates uncertainty, this was ultimately an opportunity for growth and renewal.
DEVELOPMENT OF NEW MACHINING DEPARTMENT
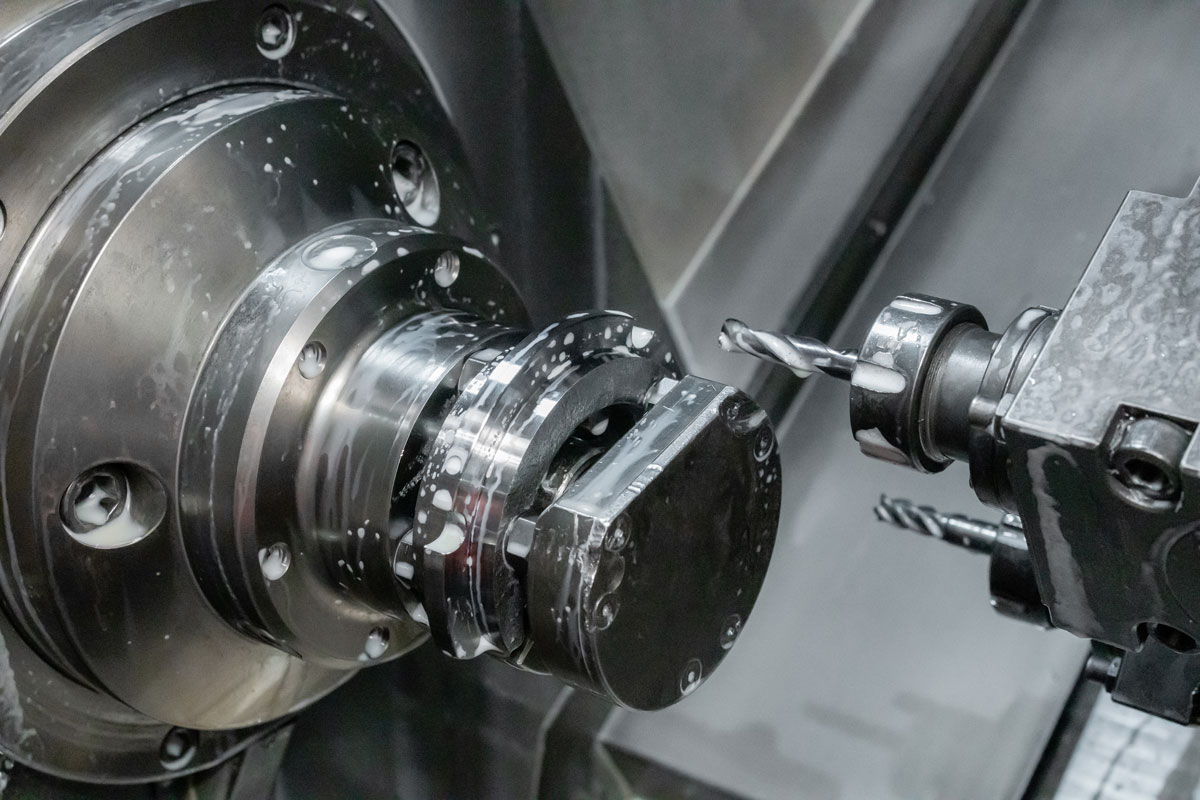
The investment in machinery for machining of parts allowed us to internalize processes that had been outsourced until then. Likewise, a new press was acquired, expanding our fleet to 4 hot forging lines, in addition to disc saws, a shot blasting machine of greater capacity and presses for cold processes.
FIRST INVESTMENT IN FORGING SIMULATION SOFTWARE
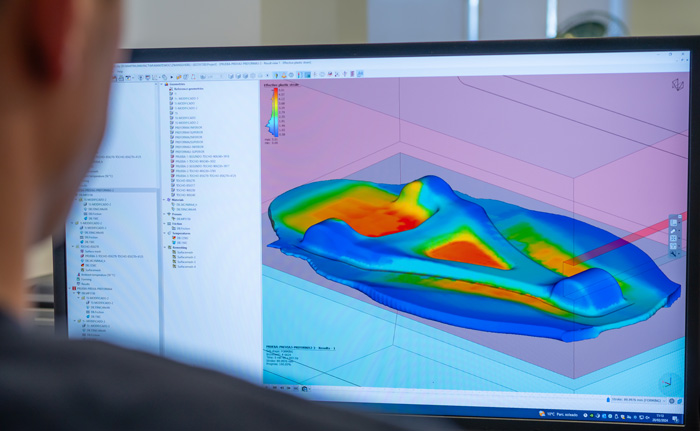
The investment in forging simulation software was essential both for designing new parts and for optimizing our production process.
It allowed us to analyze the flow of materials during forging, anticipating possible failures and improving the quality of the final product.
The materialization of this investment allowed us to reduce the time required to set up new projects, thus increasing our competitiveness in the market.
INVESTMENT IN PRESS OF 3150 AND ACQUISITION OF NEW PAVILION IN IURRETA
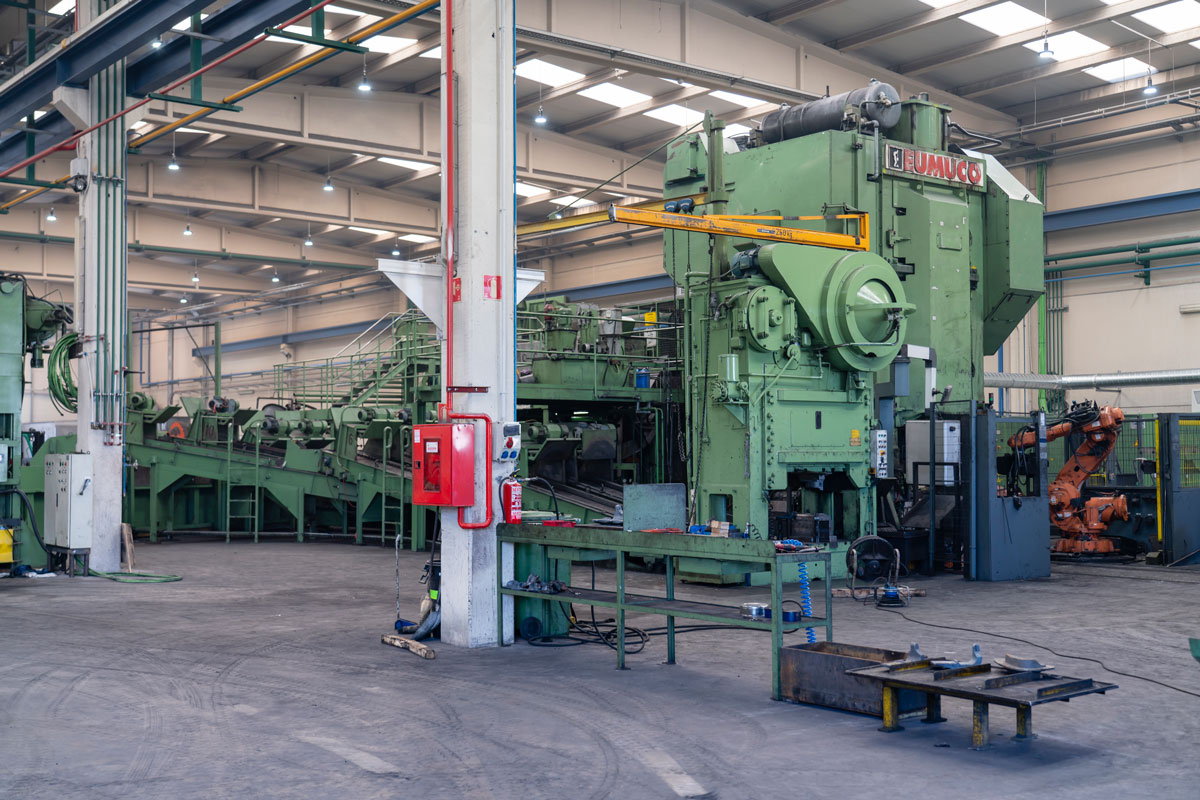
The acquisition of the 3150 press opened the door to larger parts and new sectors such as railroads and heavy machinery. At the same time, we increased our production capacity by acquiring a new plant to replace the original plant.
This strategy not only responds to current market needs, but also positions the company competitively in the industry.
ROBOTIZATION OF THE 3150 PRESS
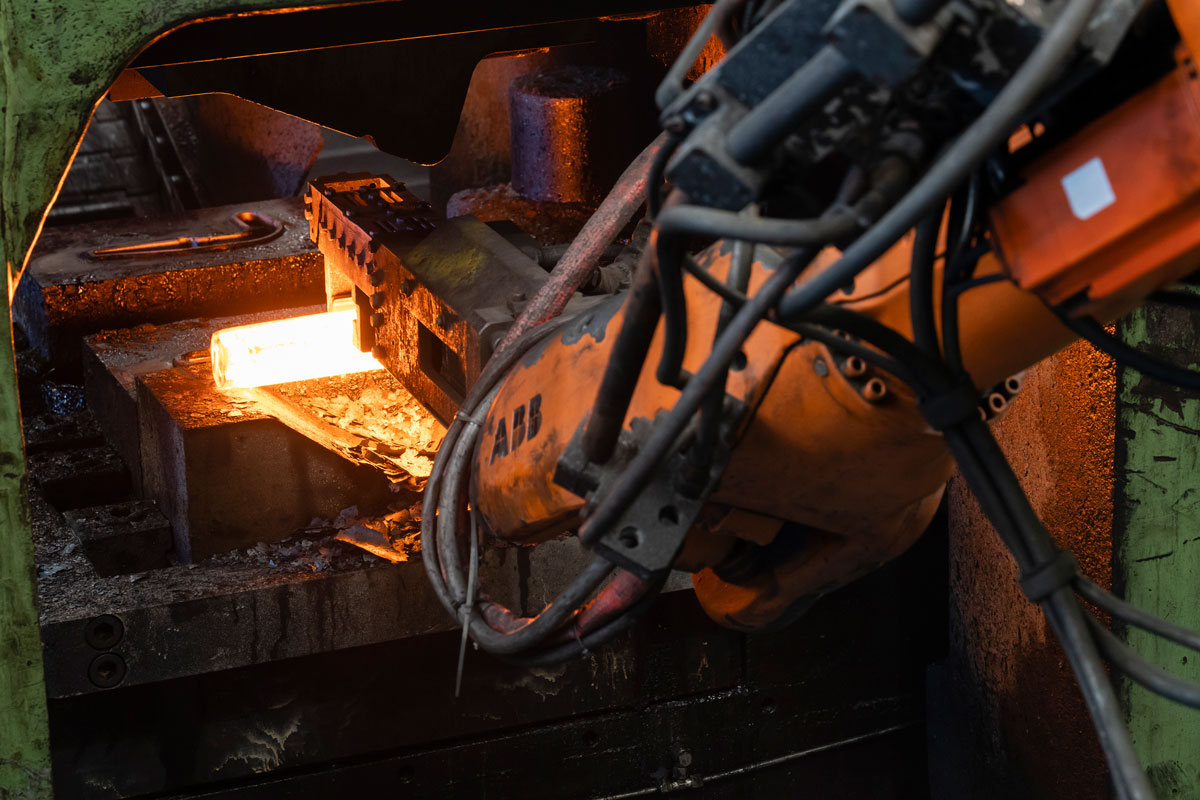
The robotization of the 3150 press represents a significant advance for our company, enabling the handling of heavier parts efficiently. This transformation requires a strong investment in specialized software, as well as the incorporation of qualified personnel equipped with the necessary skills to operate and maintain these automated systems, thus guaranteeing efficient and sustainable production over time.
WELDING ROBOT IMPLEMENTATION
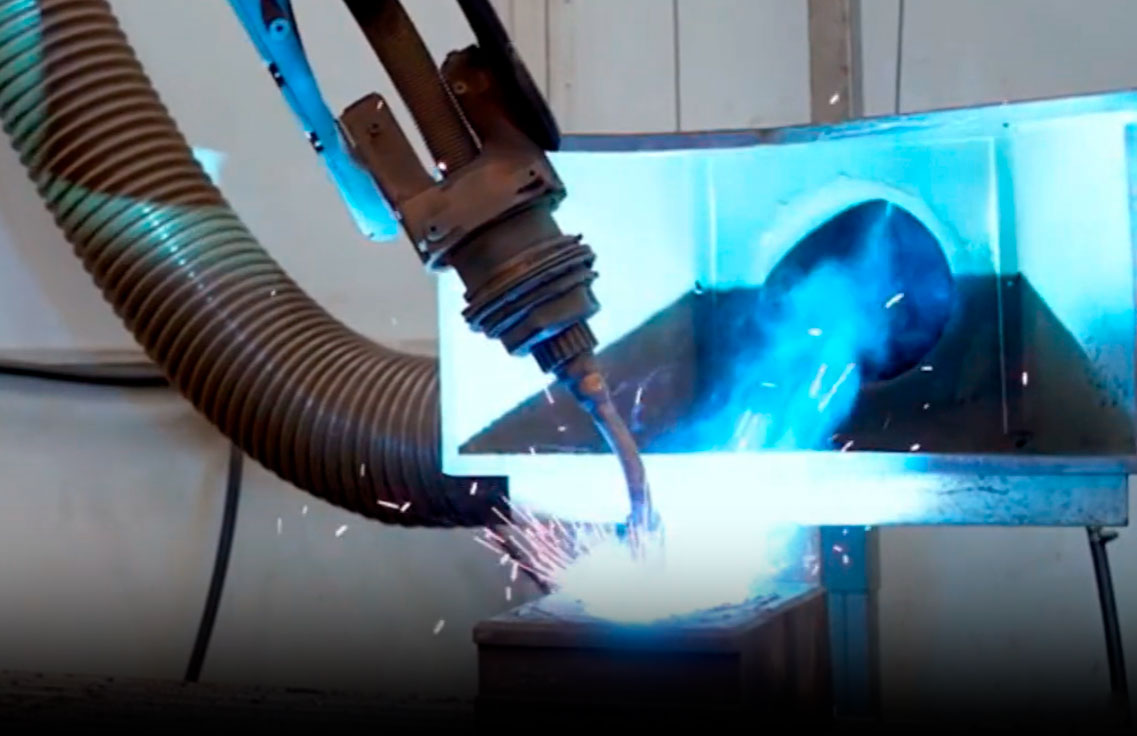
The implementation of the welding robot in die manufacturing has proven to be a fast and efficient solution to our welding capacity problems.
These automated systems optimize processes, reducing production time and improving joint accuracy.
It allows us to meet market demand with greater agility and efficiency.
Thus, its implementation represents a strategic investment in our industrial modernization.
EXPANSION OF FACILITIES
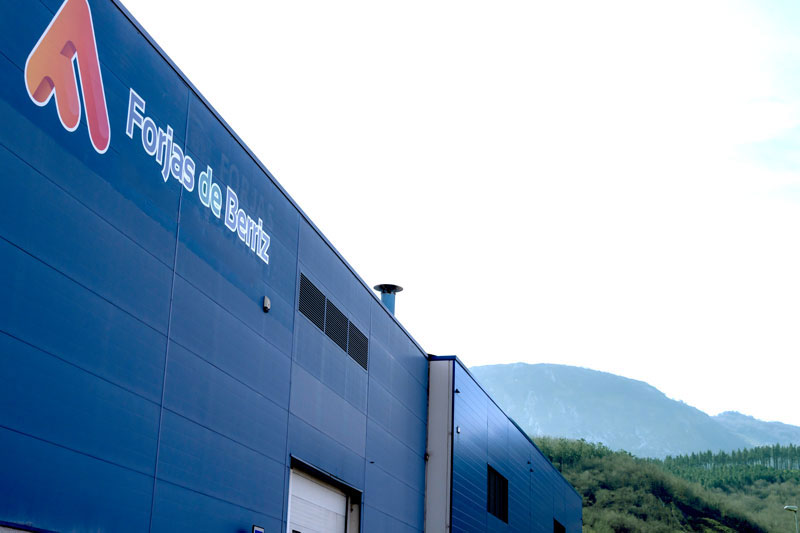
The expansion of the facilities allows us to centralize the production process in a single plant, facilitating work flow and coordination.
This expansion is aimed at increasing raw material storage space, optimizing machinery distribution, improving the plant layout and facilitating the storage of finished products and packaging, which demand more and more space due to their reusable nature.
CONSOLIDATION OF PRODUCTION IN A SINGLE PLANT
Forjas de Berriz is installed on a single floor.
It has been a long and laborious process, not without its problems, but the results have been extraordinary.
The company has significantly improved in key aspects such as the quality of its facilities, production process, layout and environmental care.
We anticipate new investments that will allow us to expand our business.